Master Unit Die is a flexible mold system for injection molding. It makes manufacturing easier with fast tool changes and switchable mold parts. This system cuts downtime by up to 75% and reduces tool costs by up to 66%. It works with different part sizes, boosting efficiency and lowering production costs.
Key Takeaways
Table of Contents
ToggleMaster Unit Die systems let molds change fast, saving time. They cut downtime by 75% and tooling costs by 66%. This helps companies save both time and money.
MUD systems have a modular design for different sizes and shapes. They work well for small or medium production runs. This makes it easy for businesses to adjust to new needs.
Buying a Master Unit Die system can save money over time. Even though it costs more at first, training and care keep it working well.
Understanding Master Unit Die
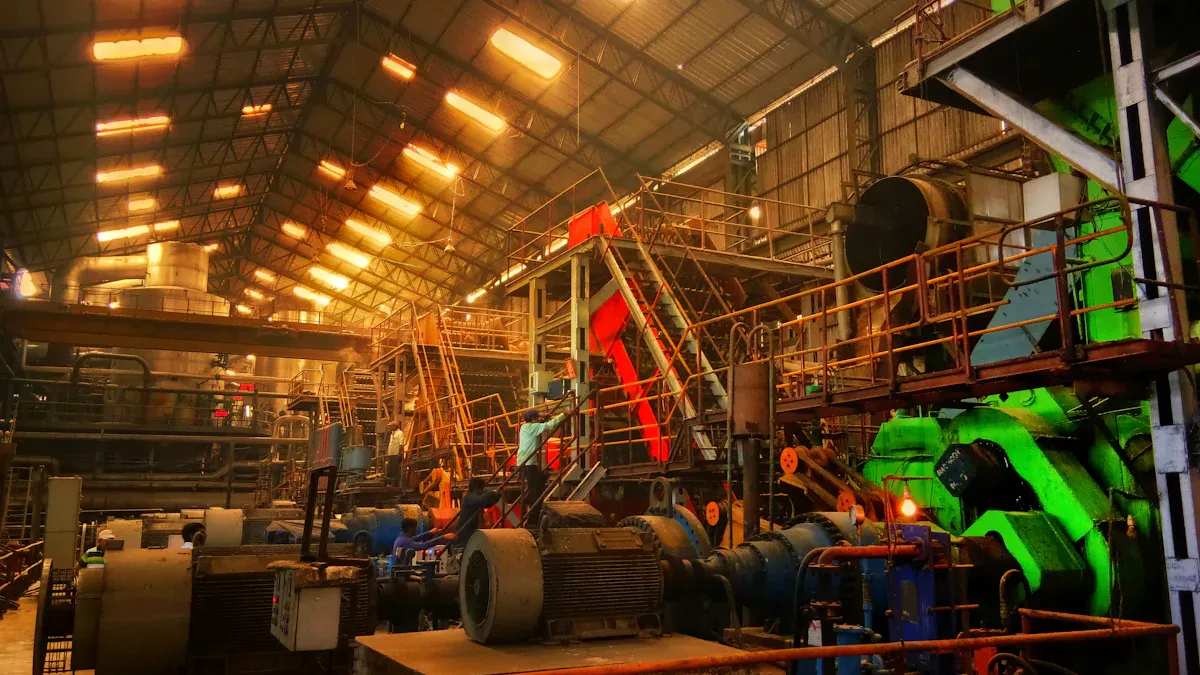
What is a Master Unit Die?
A Master Unit Die (MUD) is a special mold system. It is used in injection molding to make parts. The system has a base that stays in the machine. You can switch out inserts without removing the base. This saves time and lowers production costs.
The system uses a frame with A and B plates. These plates hold the shapes that form the final product. This setup makes the MUD system flexible and efficient.
Purpose and Applications in Manufacturing
The main goal of a MUD system is to make mold changes faster. It is popular in industries like cars, medical tools, and consumer products. It helps companies adjust production schedules quickly.
Here are some benefits of using MUD systems:
Lower costs: You only buy inserts, not the whole mold.
Faster work: Quick changes mean less downtime.
Eco-friendly: Reusing the frame reduces waste.
Custom options: Great for small production runs.
Many businesses use MUD systems to save money and time. They also help products get to market faster by focusing on core and cavity work.
Key Components of a MUD System
A MUD system has important parts that improve its use. The table below shows these parts and their roles:
Component | How It Helps |
---|---|
Quick-Change Feature | Makes switching molds fast and easy. |
Many Design Options | Offers flexibility and saves time and money. |
Faster Market Delivery | Uses pre-made frames to cut machining time. |
Flexible Supply Chain | Helps with quick production schedule changes. |
Customization | Works well for small, low-cost production runs. |
These parts work together to make the MUD system useful. It helps manufacturers work faster and more efficiently.
How Master Unit Die Works
The Quick-Change Process
One great feature of the Master Unit Die system is its quick-change process. You can swap mold inserts without taking out the whole frame. This saves a lot of time and keeps production running smoothly. Downtime can drop by up to 75%, and tooling costs can go down by 66%.
The design makes changing molds fast and simple. You can replace inserts easily, keeping your work on track. This is especially helpful in industries like car making and consumer goods, where time is very important.
Metric | Improvement |
---|---|
Downtime Reduction | Up to 75% |
Initial Tooling Cost Savings | Up to 66% |
Interchangeable Mold Inserts
Interchangeable inserts are a key part of the Master Unit Die system. These inserts let you change molds quickly to meet new production needs. Unlike old-style molds, you only switch the inserts, not the whole frame. This cuts setup time from hours to just minutes, reducing delays.
The system also saves money. You only buy inserts, not a full mold base. Plus, reusing the frame helps cut waste, making it eco-friendly. This flexibility is perfect for small jobs or when you need to launch products fast.
Benefit | Description |
---|---|
Reduced Setup Time | Cuts setup time from hours to minutes, boosting efficiency. |
Quick Modifications | Easy changes without removing the frame, saving time. |
Cost-Effectiveness | Saves money by only needing inserts, not full mold bases. |
Enhanced Sustainability | Reusable frames reduce waste and support eco-friendly practices. |
Integration with Injection Molding Machines
The Master Unit Die system works well with many injection molding machines. Its modular design fits different part sizes and shapes. This means you can use it for various projects without big changes.
The system helps manufacturers save time and work more efficiently. Pre-made frames let you focus on the main mold parts, speeding up production. The quick-change feature also supports just-in-time production, helping manage inventory better.
Feature | Description |
---|---|
Versatility | Works with many part sizes and shapes. |
Quick Tooling Changes | Fast changes reduce downtime and improve productivity. |
Modular Design | Fits different machines for smoother operations. |
Lean Manufacturing Support | Boosts uptime and lowers costs, matching lean production goals. |
Features and Benefits of Master Unit Die
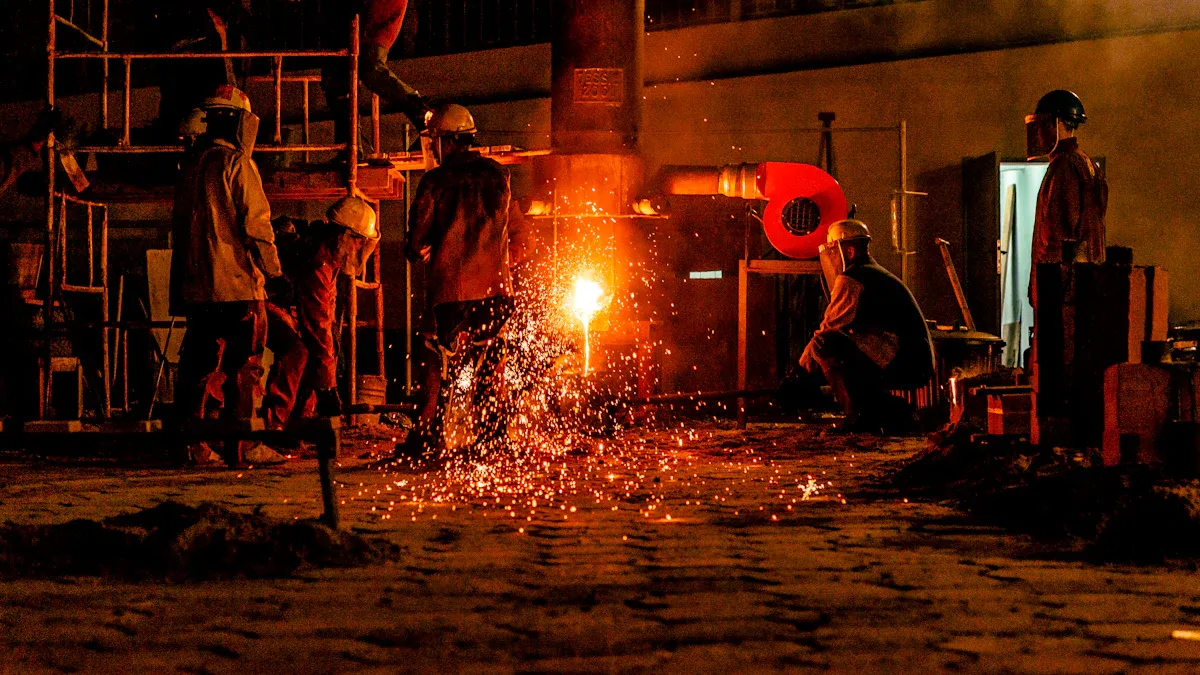
Key Features of MUD Systems
Master Unit Die systems have features that improve injection molding. They work with hot runner systems, which help materials flow better and reduce waste. The double H series frame lets you mold four inserts at once, increasing productivity. You can also connect the ejector system to the master frame using an interlocking rail for smoother operations.
Another great feature is the MUD Quick-Change E-Frames. These have a center runner bar, allowing two insert molds to work together. They support both injection and transfer molding, making them useful for many tasks. The companion insert molds come in U-Frame and T-Style designs, giving more options for different needs.
Feature/Specification | Description |
---|---|
Works with hot runner systems | Yes |
Double H series frame | Molds four inserts at the same time |
Ejector system | Connects to master frame with interlocking rail |
MUD Quick-Change E-Frames | Has a center runner bar for two companion insert molds |
Applications | Supports injection and transfer molding |
Advantages in Cost and Efficiency
Master Unit Die systems save money and improve efficiency. The modular design allows quick insert changes, cutting downtime by up to 75%. This also reduces labor costs since less time is needed for mold changes. Initial tooling costs drop by up to 66% because you only buy inserts, not full mold bases.
Compared to regular mold systems, MUD systems are more flexible and cost-effective. The table below shows these benefits:
Feature | MUD System Benefits | Standard Mold Systems |
---|---|---|
Downtime Reduction | Up to 75% less downtime | Not specified |
Initial Tooling Cost | Up to 66% cheaper | Not specified |
Flexibility | Modular design for fast changes | Fixed design |
Labor Cost | Lower due to quick-change inserts | Higher due to longer changes |
Flexibility for Small and Medium Production Runs
MUD systems are great for small and medium production runs. Their modular design makes it easy to adjust to new production needs. You can swap inserts to make different parts without buying new mold bases. This is helpful for businesses making many product types or launching new items quickly.
The system works with various sizes and shapes, adding to its usefulness. Standard insert molds come in solid or laminated designs, including three- and four-plate options. Sizes range from 05/05 to 18/26, so you can find one that fits your needs. This flexibility makes MUD systems a smart, cost-saving choice for manufacturers wanting to stay competitive.
Challenges of Using Master Unit Die
Initial Investment and Setup Costs
Starting with a Master Unit Die (MUD) system can cost a lot. You need to buy the master frame, inserts, and extra tools. While it saves money later, the upfront cost may seem high. This can be tough for small businesses or startups.
Tip: Think about the long-term savings in time and money. The system often pays for itself over time.
You also need skilled workers to set up the system. Training your team to use the quick-change process adds to the cost. But once trained, your team will work faster, making the system worth it.
Mold Design Complexity
Making molds for a MUD system is harder than regular molds. The inserts must fit perfectly into the master frame. Even small mistakes can cause delays or bad parts.
To fix this, hire expert mold designers or use good software. These tools help you make accurate designs that work well with the system.
Challenge | Solution |
---|---|
Perfect Insert Fit | Hire experts or use advanced design software. |
Risk of Errors | Test molds carefully before starting full production. |
Maintenance and Compatibility Considerations
Keeping a MUD system running needs regular care. Check the master frame, inserts, and ejector systems often. Skipping maintenance can lead to expensive repairs or delays.
Another issue is compatibility. Not all machines work well with MUD systems. Before buying, make sure your machine supports the system’s design.
Note: Regular checks and ensuring compatibility are key to keeping your MUD system efficient and long-lasting.
Master Unit Die makes injection molding easier with its modular design. It saves time and money by allowing quick mold changes. The system uses interchangeable inserts and works with many machines. Though it needs upfront investment and care, the benefits last long. It’s a smart choice for affordable and modern manufacturing.
FAQ
What industries gain the most from using Master Unit Die systems?
Industries like cars, medical tools, and consumer products benefit greatly. These fields need fast production changes, lower costs, and flexibility for smaller jobs.
How does a MUD system save time in production?
The quick-change feature lets you switch inserts in minutes. This cuts downtime by up to 75%, keeping production on schedule.
Can all injection molding machines use a MUD system?
Not every machine works with it. Check your machine’s specs to see if it fits the MUD system’s modular design.
Tip: Ask your machine’s maker about compatibility before buying a MUD system.