Choosing the right material for your Apple Watch band can significantly impact customer satisfaction, compliance risks, and your profit margin.
As a professional Apple Watch bands supplier, we analyzed the advantages, disadvantages, and hidden costs of each material. Using this guide can help you negotiate better with manufacturers and avoid costly mistakes.
Why is Material Selection Important for Your Business
Table of Contents
ToggleMore than 58% of consumers in the United States and the European Union now prioritize eco-friendly materials (Statista, 2025). If you choose the wrong option, you may face the risk of returns, recalls, or sales losses. Compliance failure can result in a loss of up to $50,000 per batch of goods, and we have witnessed this happen. Work with a reliable Apple Watch bands manufacturer who understands the following 4 key factors:
- Durability (sweat/UV resistance)
- Certifications (REACH, FDA, LWG)
- Production Scalability
- Total Cost (not just unit price)
Comparison of Different Apple Watch Band Materials
1. Silicone: The Most Widely Used Material
Each major supplier of Apple Watch bands offers silicone material, but the quality varies.
- Advantage: Costs just 0.80−0.80−1.20/piece at 5k MOQ. Withstands -40°C to 220°C. It has excellent waterproof performance and is an ideal choice for a waterproof Apple watch band.
- Disadvantages: using inferior silica gel or a dirty production environment may cause skin allergy to consumers, thus affecting your sales and brand reputation. Therefore, it is required that your supplier provide ISO 13485 certification, which is an internationally recognized quality management standard that meets the standards of medical devices.
- Essential for manufacturers: LSR technology. It is safe, non-toxic, waterproof, and capable of meeting food-grade requirements, preventing suppliers from using outdated rubber molding technology.
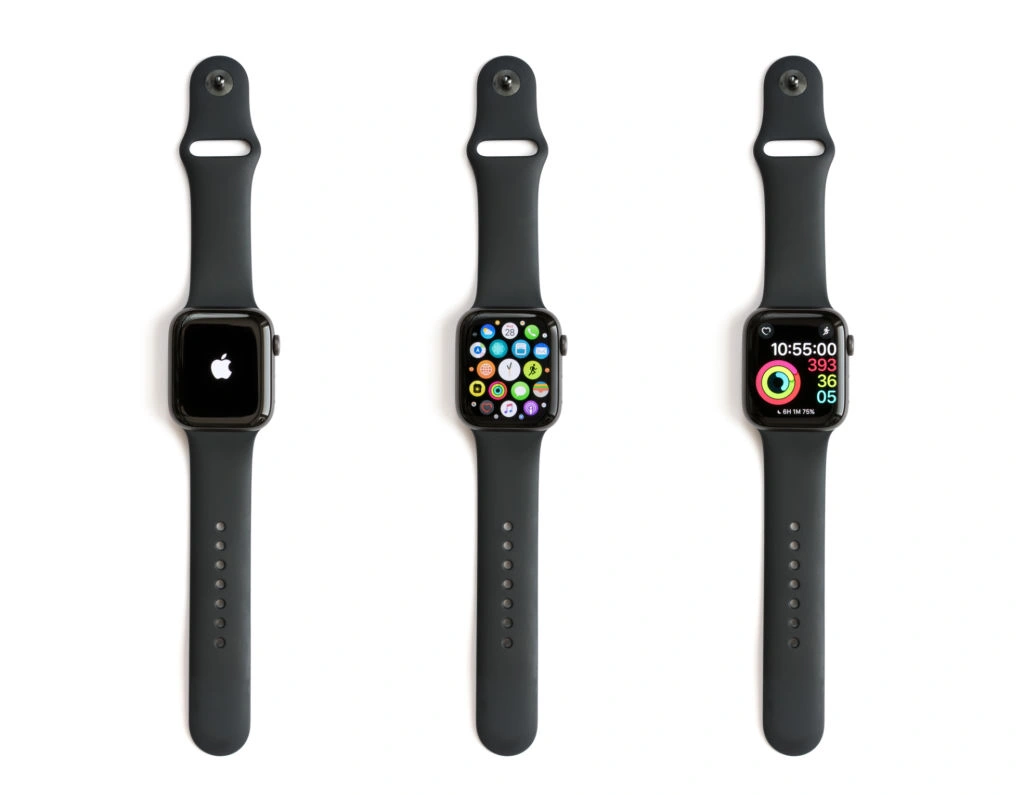
silicone apple watch bands
2. Leather: Luxury Demand, Complex Sourcing
A high-quality leather band for the Apple Watch needs a traceable origin.
Advantages:
- Leather watch bands can enhance the grade of watches, and their price is more than three times that of silicone ones.
- Leather is soft and breathable, making it suitable for both daily and business occasions.
- When using recycled leather or plant tanning processes, the environmental impact can be reduced. EU buyers need LWG-certified leather.
- Classic Durability: High-quality leather (such as full-grain leather) can last for several years in a dry environment if properly maintained.
Disadvantages:
- Leather is susceptible to environmental influences, which can lead to a shortened lifespan (averaging only 2 to 3 years, compared to over 10 years for metal watch bands).
- Leather requires regular maintenance, which is demanding and costly.
- Genuine leather is expensive, and an unstable supply chain may lead to production disruptions or profit compression.
Compared with silicone or metal bands, leather bands are more prone to wear and tear or scratches. Perform poorly in sports or outdoor scenarios.
Manufacturers must have:
- Strict material selection and supply chain management: Priority is given to certified leather to ensure no harmful chemical residues (in compliance with REACH regulations); Establish a diversified supplier network to avoid risks from a single source.
- Strengthen process quality control: During the production process, ensure that the products meet the ISO 9001 standard and reduce the defect rate.
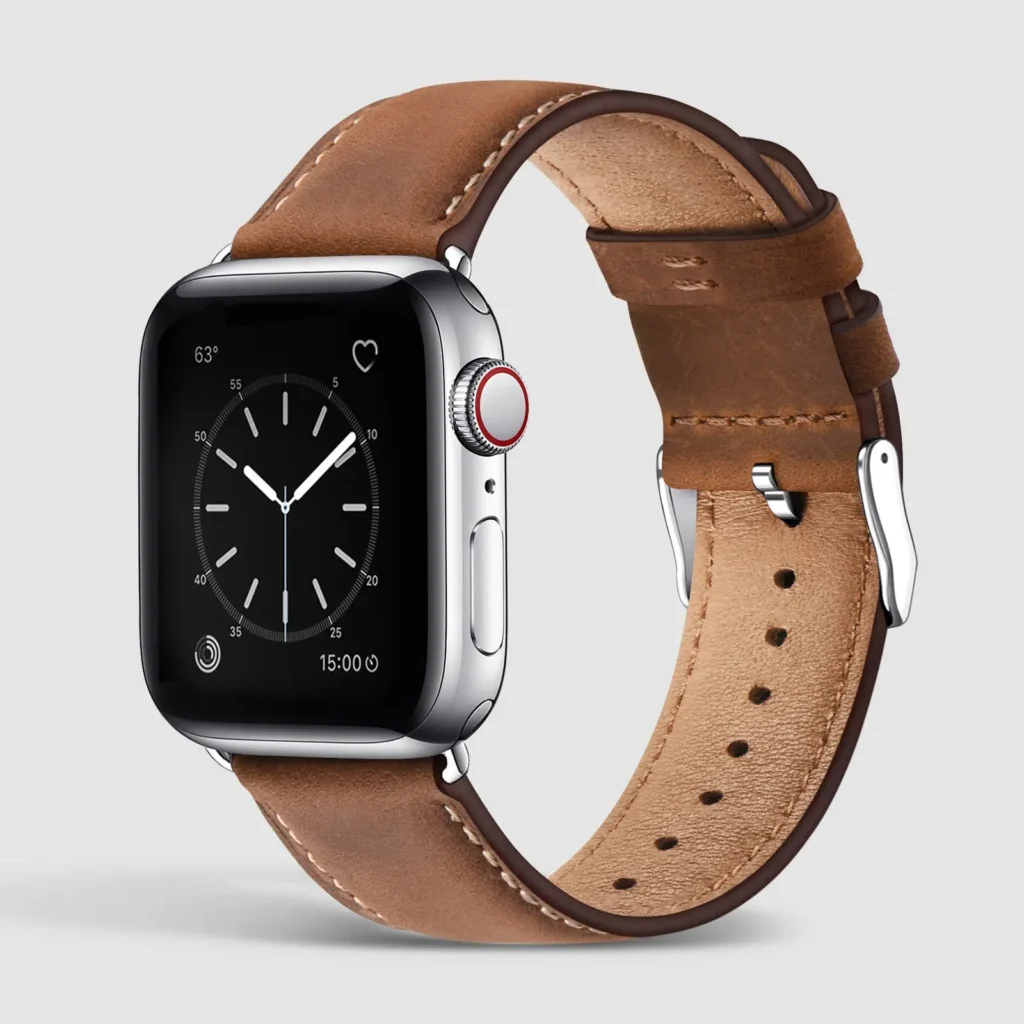
Leather apple watch bands
3. Stainless steel and titanium: Good durability
Metal watch bands attract high-income buyers, but they require precise engineering design.
Advantage:
- 316L medical grade stainless steel service life can reach more than 10 years, with almost no maintenance (only occasionally wipe), and low maintenance cost.
- Waterproof, sweat-proof, and resistant to high and low temperatures (stable from -50℃ to 300℃). The surface can achieve medical-grade cleanliness through electrolytic polishing, avoiding skin allergies and meeting the EU REACH standards.
- Stable raw material costs, 100% recyclable, in conjunction with ESG policy requirements.
- Supports precision processing (CNC engraving, laser etching) and multi-surface treatment (brushing, mirror finishing, IP vacuum electroplating).
Disadvantage:
- CNC machining costs 4.50(steel) to 12.00 (titanium) per band. Polishing defects cause returns.
- Comfort and adaptability limitations, winter wear, cold, not so close to the wrist, leather.
Manufacturer Must-Have:
- Give priority to using low-carbon 316L stainless steel (to reduce nickel sensitization) or titanium alloy (50% lighter weight)
- 5,000-cycle magnetic clasp testers. Demand #600+ grit polish samples.
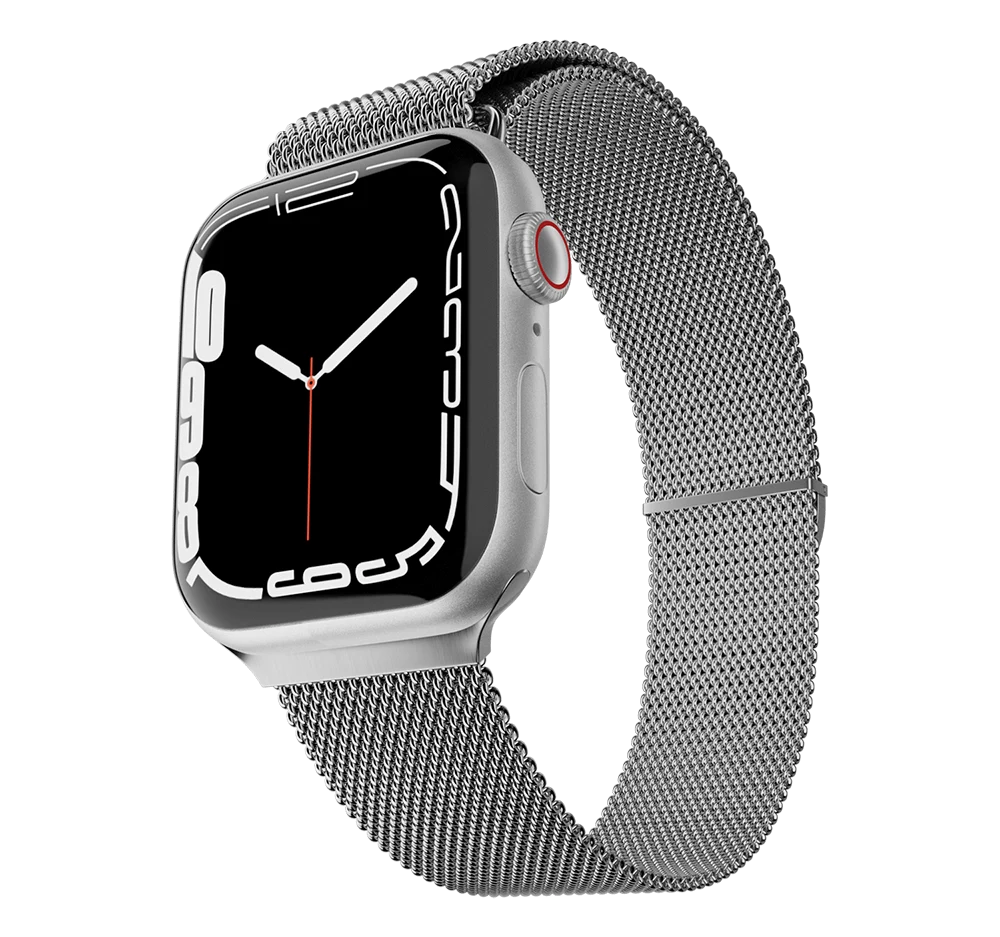
Metal apple watch bands
4. Eco-TPU/Nylon: The Rising Stars
67% of wholesalers now demand sustainable options.
Advantages:
- Recycled nylon material is derived from Marine plastics and can effectively protect the Marine environment. Plant-based TPU reduces carbon footprint.
- Recycled TPU injection molding efficiency supports a variety of customized effects to meet individual needs.
- Regenerated nylon is lightweight yet strong and very durable.
Disadvantages:
- Regenerated nylon shrinks by 2% compared to the original nylon. Special bonding adhesives are required.
- Regeneration moisture content up to 4% (TPU only 0.5%), humid environment easy to breed bacteria.
Manufacturer Must-Have:
- Material traceability documents.
- Passed strict antibacterial tests and provided maintenance guidelines.
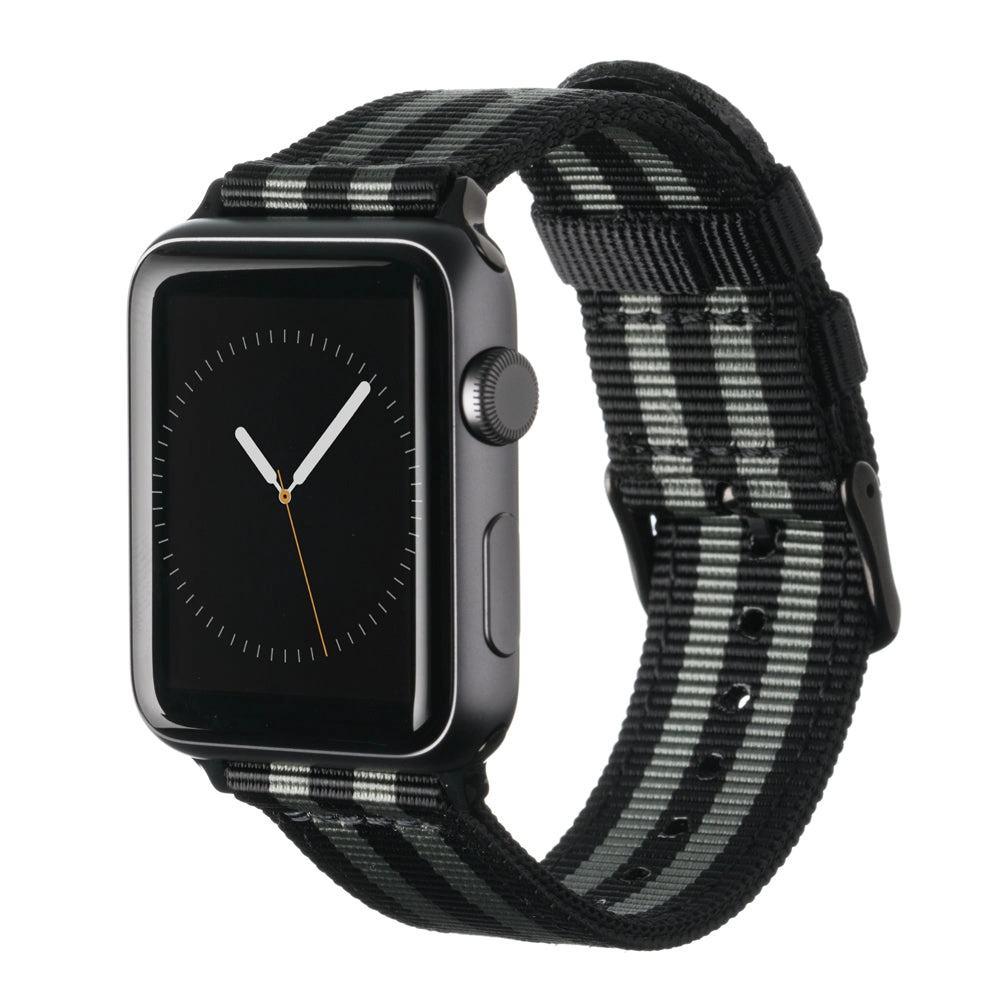
Eco Nylon apple watch bands
Material Comparison Table
Material | Cost per Unit (5k MOQ) | Lead Time | Key Certification | Best For |
---|---|---|---|---|
Medical Silicone | 0.80−0.80−1.20 | 25 days | FDA 21 CFR 177.2600 | Waterproof Apple Watch band |
LWG Leather | 8.50−8.50−12.00 | 45 days | LWG Gold | Best Apple Watch leather bands |
316L Steel | 4.50−4.50−6.00 | 30 days | RoHS/REACH | Magnetic watch band for Apple Watch |
GRS Nylon | 1.70−1.70−2.50 | 28 days | GRS v3.0 | Eco-conscious lines |
5 Must-Ask Questions for Your Manufacturer
Don’t sign contracts without verifying these:
- “Show me your REACH SVHC 235 test report for this material.” (Avoids EU customs holds)
- “What’s your daily LSR output capacity?” (Exposes production bottlenecks)
- “Do you offer 3D printing + physical samples in 7 days?” (Tests responsiveness)
- “Can we start with 1,000 custom Apple Watch bands?” (Avoids MOQ traps)
- “What’s your defect rate for metal clasp fatigue tests?” (Target: <0.5%)
Future-Oriented Procurement Strategies
A. Hybrid material solutions
Value enhancement by mixed materials:
- Silicone + Recycled Nylon: Compared with full leather, the cost is reduced by 22%. Ideal for most comfortable Apple Watch band designs.
- Titanium + Plant-Based TPU: Reduce weight by 38%.
B. Small-Batch Customization
The low minimum order quantity for faster market testing:
We offer 1,000 custom Apple Watch bands, which are 50% faster than the industry average.
- Get Pantone-matched silicone Apple Watch band samples in 72 hours.
C. Compliance Safeguard Measures
Protect shipments with these clauses:
- Third-party SGS testing rights
- On-site factory audits (we provide remote video audits)
Partner with YG
As a top Apple Watch band manufacturer, we solve your 3 biggest headaches:
- Production speed: Prototype production within 72 hours (industry average 15 days).
- Compliance: Complete REACH/FDA/MFi documents.
- Flexibility: The minimum order quantity for customizing Apple Watch bands is 1,000 pieces.
Start Your Partnership Today! Contact us to build your next best-selling Apple Watch bands collection in 72 hours!
FAQ
Q: Which material is best for waterproof Apple Watch bands?
A: Medical-grade silicone (FDA 21 CFR 177.2600). Avoid stitched leather.
Q: How to verify a reliable Apple Watch bands supplier?
A: Demand 3 things: 1) Factory audit videos 2) Material certs 3) 5,000-cycle test reports.
Q: What makes the most comfortable Apple watch band?
A: Perforated eco-TPU + breathable nylon weave. 43% lighter than silicone.