Introduction
Table of Contents
ToggleFor brands sourcing waterproof phone cases, durability is non-negotiable. A single design flaw—like microscopic gaps in seams—can lead to water damage, returns, and reputational risks. While material selection is critical, the precision of injection molding often determines whether a waterproof phone case truly lives up to its claims.
This article explains how advanced injection molding technology minimizes defects in waterproof cases, and what to look for when partnering with a phone case manufacturer.
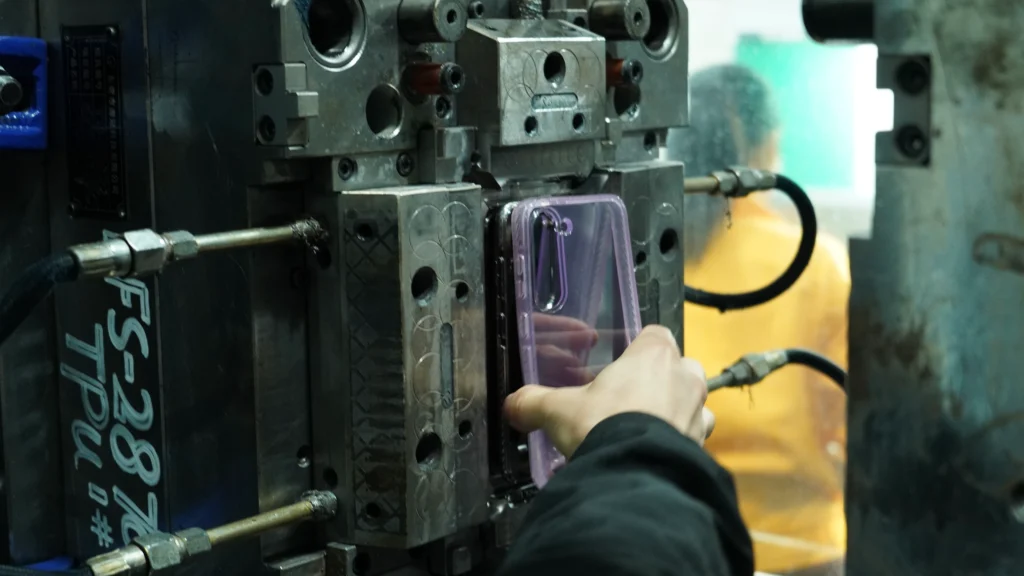
Why Injection Molding Precision Matters for Waterproof Cases
Waterproof phone cases rely on airtight seals to protect devices from moisture. Even a 0.1mm deviation in mold alignment or uneven material flow during production can create gaps, compromising the IP67/IP68 rating.
Key challenges addressed by precision molding:
Seam Integrity: High-precision molds ensure uniform wall thickness and seamless edges, eliminating potential leakage points.
Material Distribution: Consistent pressure and temperature control prevent air bubbles or weak spots in critical areas like button covers.
Dimensional Accuracy: Tight tolerances (±0.02mm) guarantee perfect fitment for specific phone models, avoiding loose fits that trap water.
How Leading Waterproof Phone Case Manufacturers Achieve Precision
Not all factories invest in the equipment or expertise needed for high-accuracy production. Here’s what sets reliable Phone Case Factories in China apart:
1. Advanced Machinery for Diverse Needs
A manufacturer’s injection molding machines determine their capability to handle complex designs. For example:
Small-Tonnage Machines (120T-250T): Ideal for slim, low-profile cases requiring delicate details.
Large-Tonnage Machines (350T-450T): Necessary for rugged cases with reinforced corners and multi-layer structures.
Example: Factories equipped with Japanese Sumitomo or Niigata machines typically deliver superior repeatability due to closed-loop pressure control systems. Meanwhile, Haitian and Multiplas machines offer cost-effective solutions for mid-volume orders without sacrificing precision.
2. Mold Design and Maintenance
Tool Steel Quality: Hardened steel molds (e.g., DIN 1.2344) resist wear, maintaining accuracy over 500,000+ cycles.
Real-Time Monitoring: Sensors detect mold temperature fluctuations or material flow inconsistencies, enabling immediate adjustments.
3. Rigorous Testing Protocols
Reputable waterproof phone case manufacturers validate precision through:
CMM (Coordinate Measuring Machine) Scans: To verify dimensional accuracy against CAD models.
Pressure Chamber Tests: Simulating IP68 conditions (1.5m depth for 30 minutes) to identify even minor leaks.
The Hidden Costs of Poor Injection Molding Precision
Choosing a factory solely for low costs can backfire. Common issues include:
Higher Defect Rates: Substandard molds may cause 5-10% of units to fail waterproof tests, increasing per-unit costs.
Longer Lead Times: Reworking defective batches delays shipments, impacting your time-to-market.
Brand Liability: A 2023 Retail Dive survey found that 43% of consumers would publicly share negative experiences with faulty waterproof products.
What to Ask Potential Suppliers
To avoid these risks, evaluate a phone case manufacturer with these questions:
“What is your mold tolerance standard, and how is it measured?”
Look for: Tolerance levels ≤ ±0.05mm and CMM reports.
“Can you provide examples of waterproof cases you’ve produced for similar brands?”
Request: Test videos or third-party certification records.
“How do you maintain machine accuracy over time?”
Expect: Scheduled calibration logs and preventive maintenance plans.
Case Study: Precision in Action
A European outdoor brand needed IP68-rated cases for extreme environments but faced recurring leaks from their previous supplier. After switching to a factory with multi-tonnage Sumitomo machines and CMM validation, their defect rate dropped from 8% to 0.5%, saving €120,000 annually in replacement costs.
Conclusion
Injection molding precision isn’t just a technical detail—it’s the foundation of waterproof phone case reliability. By partnering with a Phone Case Factory in China that prioritizes advanced machinery, meticulous mold design, and transparent testing, brands can reduce risks and build trust with quality-conscious consumers.
Need a Partner Who Balances Precision and Durability?
[Explore how YG 130+ injection molding machines, including Sumitomo, Niigata, and Haitian systems, ensure airtight waterproof cases].