Introduction
Table of Contents
ToggleA North American tech company specializing in next-generation AR/VR headsets aimed to enhance user experience through lightweight design and high-precision components. Facing an industry growing at 40% annually, the client needed to complete product development and mass production within 5 months. However, traditional mold manufacturing’s long lead times and high costs became critical bottlenecks. Leveraging our MUD Rapid Mold Service and end-to-end injection molding solutions, the client overcame technical barriers and seized market opportunities.
The Challenge: Core Pain Points in AR/VR Manufacturing
- Demand for Rapid Iteration: Competitors compressed development cycles to 6 months, while the client’s traditional mold development required 10 weeks, delaying product launches.
- Balancing Precision and Lightweighting: Optical component assembly demanded mold tolerances ≤02mm and materials with density <1.1g/cm³.
- High Costs for Small-Batch Pilots: Initial orders of 1,000 units saw traditional mold costs consuming 50% of the development budget, straining R&D resources.
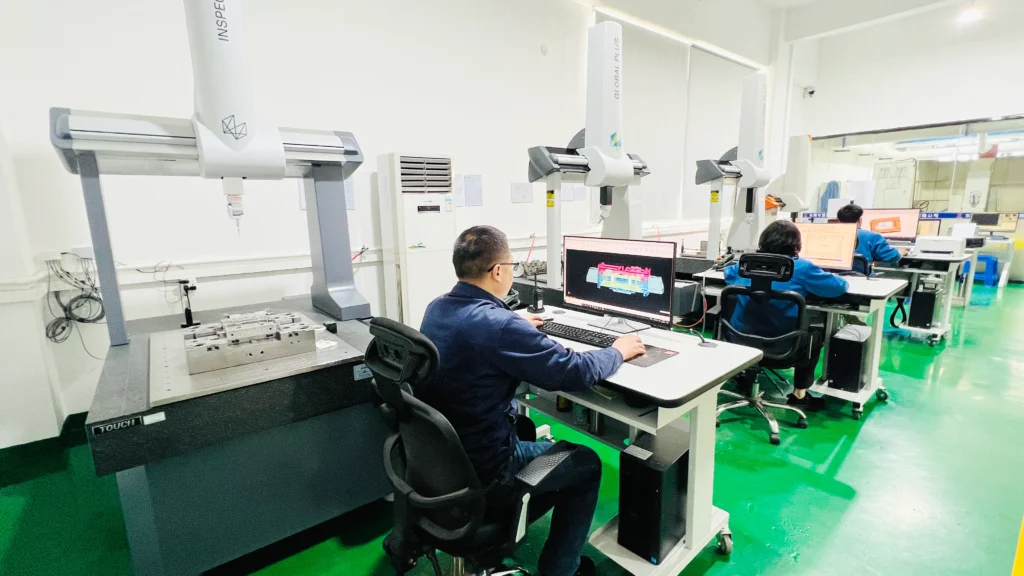
The Solution: MUD Rapid Mold Service & Customized AR/VR Support
As a trusted partner in AR/VR manufacturing, we delivered the following innovations:
- MUD Rapid Mold Service
- 15-Day Mold Delivery: Aluminum molds and high-speed machining reduced traditional steel mold development from 10 weeks to 15 days, enabling rapid design validation.
- 40% Cost Reduction: Modular design and standardized component reuse lowered pilot-phase mold costs to 60% of industry averages.
- Ultra-Precision Injection Molding
- Five-axis CNC machining and mirror electroplating achieved mold surface roughness of Ra0.05μm, ensuring flawless optical component assembly.
- Custom glass-fiber-reinforced PA66 material reduced weight by 35% while achieving 120MPa flexural strength for long-term durability.
- Agile Supply Chain Support
- Small-Batch Flexible Production: Orders as low as 500 units, with 25-day end-to-end delivery (mold development + first batch production).
- Full-process automated inspection ensured 100% compliance with IP68 waterproofing and 1.8m drop tests, with defect rates below 0.3%.
- Value-Added Services
- Hot runner optimization and material recycling reduced waste by 25%, cutting per-unit costs by 20%.
- CE/FCC certification support accelerated market entry in the U.S. and EU.
Results: Efficiency and Performance Breakthroughs
- Faster Development: The client’s product cycle shortened from 10 months to 6 months, enabling 3 annual iterations.
- Cost Optimization: Total mold costs dropped by 45%, freeing budgets for core sensor R&D and performance upgrades.
- Market Success: The first product captured 12% of the North American market within 3 months, with a user satisfaction score of 4.8/5.0.
- Industry Recognition: Awarded the 2024 “Global Wearable Tech Innovation Award,” with unboxing videos surpassing 1.8 million views.
Client Testimonial
“The MUD Rapid Mold Service revolutionized our workflow. Receiving functional molds in 15 days was unimaginable before. Their end-to-end solutions saved costs and gave us a critical time-to-market edge.”
— Product Director
Bring Your AR/VR Device to Market Faster
Whether you need MUD Rapid Molds, high-precision molding, or global compliance support, YG offers full-spectrum services from design to delivery.
Innovate with Technology—Stay Ahead of the Competition!