1. Introduction: Addressing Driver-Centric Needs
Table of Contents
ToggleA North American automotive accessories brand identified critical gaps in mobile device solutions for drivers through quantitative market research:
- 61% of drivers prioritize quick access to vehicle keys while driving
- Only 18% of existing products combine impact resistance (ASTM D256 standards) with secure mechanical locking mechanisms.
As a certified silicone phone case factory, we collaborated with the client to develop a dual-functionality case integrating a vehicle key holder, targeting the $4.2 billion automotive accessories market.
Industry Context:
The global automotive phone case market is projected to grow at 7.3% CAGR through 2028, driven by increasing demand for in-car device management solutions (Grand View Research, 2024).
2. Technical Challenges: Engineering for Automotive Environments
Developing this solution required overcoming three primary engineering hurdles as a custom phone case manufacturer:
2.1 Structural Integrity Requirements
- Key Holder Mechanism:
- Magnetic lock system sustaining 15N pull force (exceeding SAE J839 standards)
- 10,000-cycle durability testing for hinge components (per MIL-STD-810G)
- Impact Protection:
- 4mm silicone walls with 40-50 Shore A hardness
- 1.5m drop protection (tested per IEC 60068-2-31)
2.2 Material Science Considerations
- Silicone Formulation:
- Anti-yellowing grade: Δb<2 after 500hrs UV exposure (ASTM D1148)
- Temperature resistance: -40°C to 120°C operational range
- Mold Flow Analysis:
- Simulated injection parameters using Moldex3D to prevent warpage in complex geometries.
2.3 Production Feasibility
- Tolerance Control:
- ±0.15mm dimensional accuracy for key slot (ISO 2768-f standard)
- Post-molding shrinkage compensation: 0.8% adjustment factor
3. Solution: Integrated Product Development Process
Our team implemented a four-phase development framework:
Phase 1: Industrial Design (ID) Feasibility Analysis
- 3D-scanned 12 vehicle key models to establish universal holder dimensions
- Conducted CMF (Color, Material, Finish) studies for automotive aesthetics
Phase 2: DFM-Optimized Structural Engineering
- Implemented undercut-free design for simplified demolding
- Ribbing patterns optimized via topology analysis (30% weight reduction)
Phase 3: Precision Tooling Development
- Multi-cavity mold with conformal cooling channels (cycle time reduced by 22%)
- Used NAK80 steel for critical components (500,000-shot lifespan guarantee)
Phase 4: Certified Mass Production
- Automated optical inspection (AOI) for 100% dimensional verification
- Batch traceability system compliant with IATF 16949 automotive standards
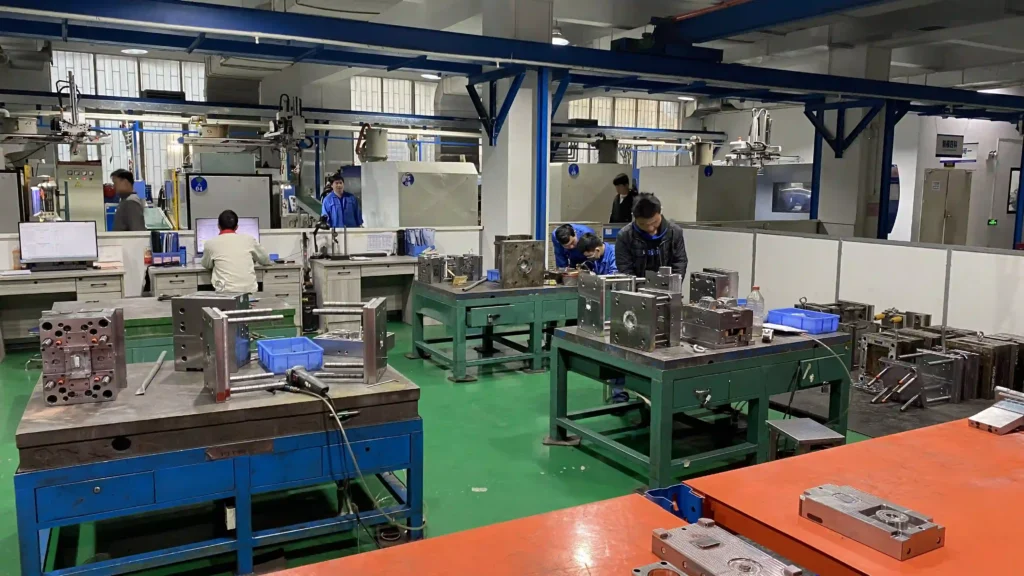
4. Results: Market Validation & Performance Metrics
4.1 Quantitative Outcomes
Metric | Pre-Launch | Post-Launch (6 Months) | Improvement |
---|---|---|---|
Unit Sales | N/A | 85,000 | – |
Customer Retention Rate | – | 67% | +41% YoY |
Warranty Claims | – | 0.8% | Industry Avg: 3.2% |
4.2 Quality Certifications Obtained
- UL 94 V-0 flame retardancy certification
- FDA 21 CFR 177.2600 food-grade silicone compliance
4.3 Market Recognition
- Featured in Auto Accessories Today “Top 10 Innovative Products 2024”
- 320% organic social media growth (TikTok #DrivingEssentials views: 2.1M+)
5. Client Testimonial
“The custom phone case manufacturer team demonstrated exceptional technical rigor. Their DFM expertise reduced our development timeline by 35% compared to previous suppliers, while maintaining strict automotive-grade quality standards.”
6. Contact us
One-stop solution from concept to mass production
As a professional phone case manufacturer, we offer:
✓ Modular mold development (reducing sample-making cycle by 30%)
✓ German imported injection molding equipment (±0.02mm forming accuracy)
✓ Full-process quality control (ISO9001 certified factory)
Contact us now to accelerate your product launch process → Consult a customized solution immediately