Introduction
Table of Contents
ToggleWhen the European fashion accessory brand Tempest Clock sought to enhance the quality of their backplate phone cases, their original supplier was unable to meet their requirements. This is not something that can be achieved simply by changing materials; it also requires a manufacturable design plan and precise processing. This poses a very significant challenge to the design teams of mobile phone case manufacturers and the requirements of the equipment.
The Challenge: Uncompromising sturdiness and processing accuracy
When they discovered YG as their backplate phone case manufacturer, they presented a complex challenge: to develop a rugged phone case with interchangeable backplate that is extremely durable while maintaining millimeter-level precision in the case’s grooves.
Their non-negotiable demands include:
- The precision of the phone case slot is guaranteed with a tolerance of ±0.03mm
- 1.5-meter drop protection (exceeding MIL-STD-810H standard)
- Supports magsafe functionality
The Solution: experienced engineering team and precision engineering
Step 1: Feasible design
After a thorough interpretation of the customer’s requirements, YG’s engineers used CAD software to provide the customer with realistic design drawings and renderings for confirmation. The core of our design is to ensure the manufacturability of the structure while matching the customer’s requirements.
1.MagSafe function design: We referred to Apple’s MagSafe specification and designed a circular magnet array precisely positioned on the back of the housing to ensure alignment with the MagSafe charger.
Step 2: Precision mold making
We process die steel materials through CNC equipment to achieve high-precision cavities. Use EDM machines to handle complex structures such as right-angle magnetic cavities and deep grooves. With the help of wire cutting machines, we process sliders and ejector pin systems to support the disassembly structure of the back plate. Finally, we assemble high-precision molds.
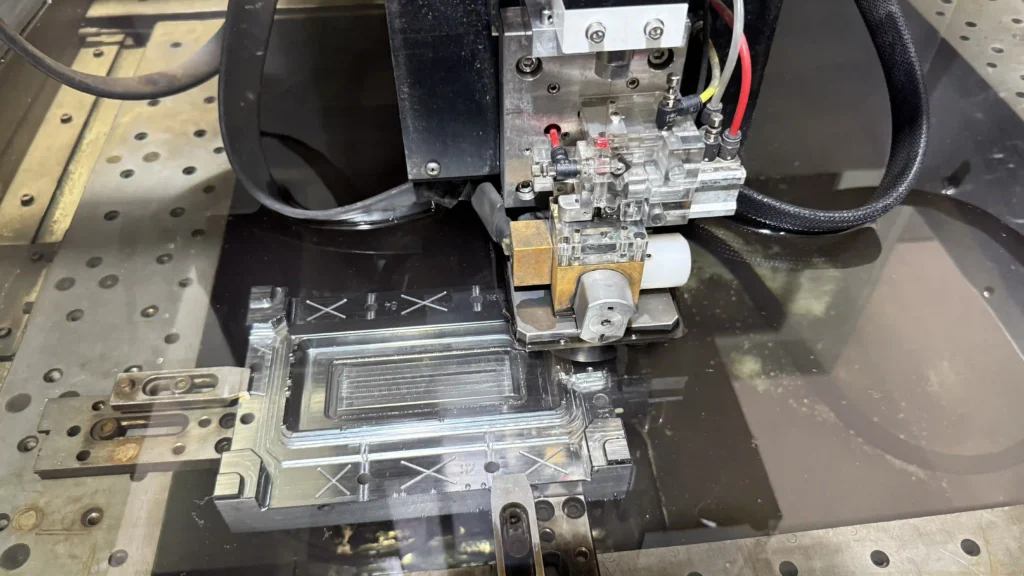
Step 3: Production and post-processing
Entering the production stage, we start the injection molding and assembly lines. The key lies in maintaining the precision and robustness of MagSafe in large-scale production, while ensuring the durability of the replaceable mechanism.
We use a multi-chamber injection molding machine and complete the injection molding in two steps:
First, the PC material is injected into the mold to form the shell skeleton, ensuring that the material is fully filled. The magnet is pre-positioned in the slot before injection molding, and its position is fixed by the molten PC coating.
Then, the TPU is re-injection molded on the PC skeleton through the plastic coating process as a buffer layer.
After the phone case is demolded, post-treatment is carried out:
- Cleaning and trimming: Remove burrs to ensure smooth snap-fit slots and prevent scratches when replacing the backplate.
- MagSafe array test: Use a magnetometer to check the magnetic attraction strength of each product (target value 12-15N).
- Interface enhancement: Add a micro silicone pad to the snap-on slot to improve wear resistance (supporting over 1,000 backplate replacements). The assembly line is fully automated, with a short time consumption (about 30 seconds per piece), ensuring consistency and efficiency.
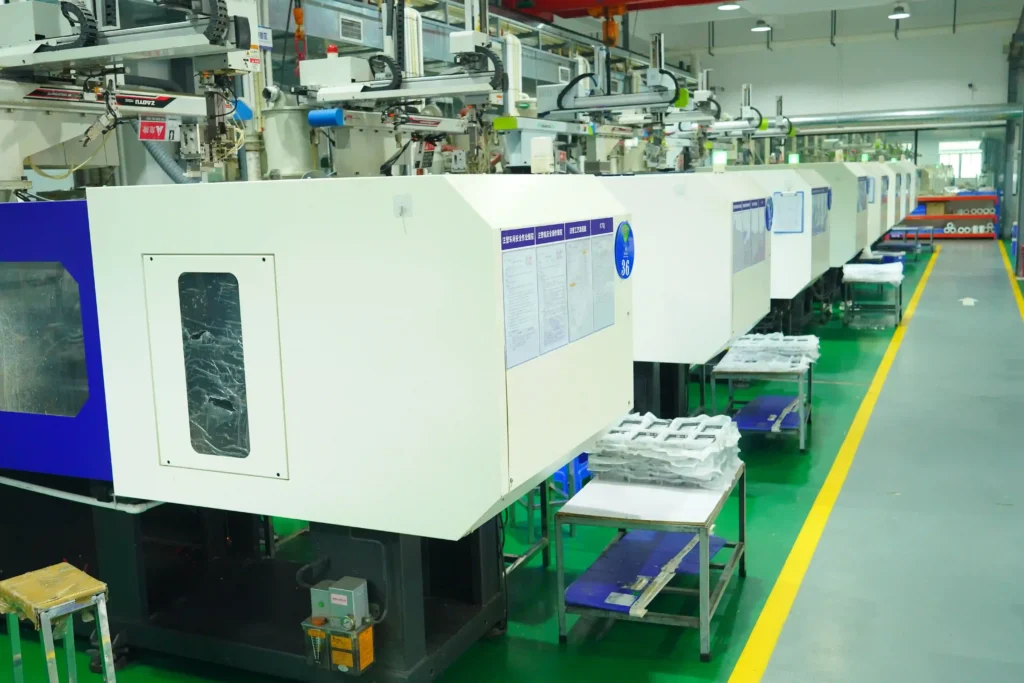
Step 4: Testing and Quality Control
Before the products come off the production line, we conduct strict tests to ensure that each housing meets the standards of MagSafe compatibility, drop resistance and reliable interfaces
Functional test:
- MagSafe compatibility: Use an Apple-certified tester to check the charging efficiency (up to 15W) and magnetic positioning (perfectly aligned with the iPhone 12-15 series).
- Drop protection test: According to the MIL-STD-810G standard, simulate a drop from a height of 1.5 meters (three times on each of the six sides). The shell must show no cracking or magnet detachment, and the phone’s integrity rate should be 99%.
Backplane replacement test: Repeatedly install/remove the standard backplane (500 cycles), and the interface must not be loose or worn.
Environmental and durability testing: including high-temperature (60°C) and low-temperature (-20°C) exposure to verify material stability; the Salt spray test is used to evaluate corrosion resistance. Daily wear simulation (such as pocket friction) ensures a service life of over 2 years.
Quality control process: Full inspection of key indicators (such as magnetic force strength), AQL sampling standard (Level II). Non-conforming products are reworked or scrapped.
Through the above four steps, we have completed the production of this batch of phone case with interchangeable backplates. The entire process took approximately 8 weeks, and the first batch production was 5,000 pieces.
Result: Market-proven success
✅ 5,000 units zero return
✅8 weeks delivery
✅ a defect rate of 0.2% crushed the customer ‘s target of 1%
✅ achieve a 30% price premium in the high-end outdoor market.
Client Testimonial: Redefining Partnership
“YG isn’t just a phone cover supplier—they’re our innovation engine.
Their 0.01mm slots fit our compass modules perfectly, and the drop test data stunned our engineering team.
10/10 for speed and precision.”
Conclusion
YG, As a professional mobile phone case factory helps our customers overcome three major challenges through professional manufacturing
- ±0.01mm ultra-precision processing (exceeding the customer’s ±0.03mm requirement)
- 1.8m military-grade drop protection certification (extreme test from -20°C to 60°C)
- The 0.2% defect rate hits a new low in the industry (50,000 sets of mass production with zero returns)
Act now, replicate success, contact us, and start the precision manufacturing of the backplate case.