Introduction
Launching a new phone case involves navigating a complex journey from design concept to market-ready product. Even minor oversights in prototyping or manufacturing can lead to delays, cost overruns, or quality failures—issues that erode brand trust and profitability. Based on insights from collaborating with global brands, we identify five critical mistakes that disrupt phone case launches and actionable strategies to avoid them.
Mistake 1: Overlooking DFM (Design for Manufacturability) Optimization
Table of Contents
ToggleThe Issue:
Many brands finalize phone case designs based solely on aesthetics or functional prototypes, neglecting manufacturing feasibility. Complex geometries (e.g., intricate textures, ultra-thin walls) may look impressive in CAD files but cause mold filling issues, sink marks, or warping during injection molding.
The Solution:
Early DFM Collaboration: Partner with a phone case manufacturer during the design phase to identify high-risk features. For example, adding draft angles to deep grooves ensures smooth demolding.
Simulation Tools: Use mold flow analysis to predict air traps or uneven cooling, reducing trial iterations by 50%.
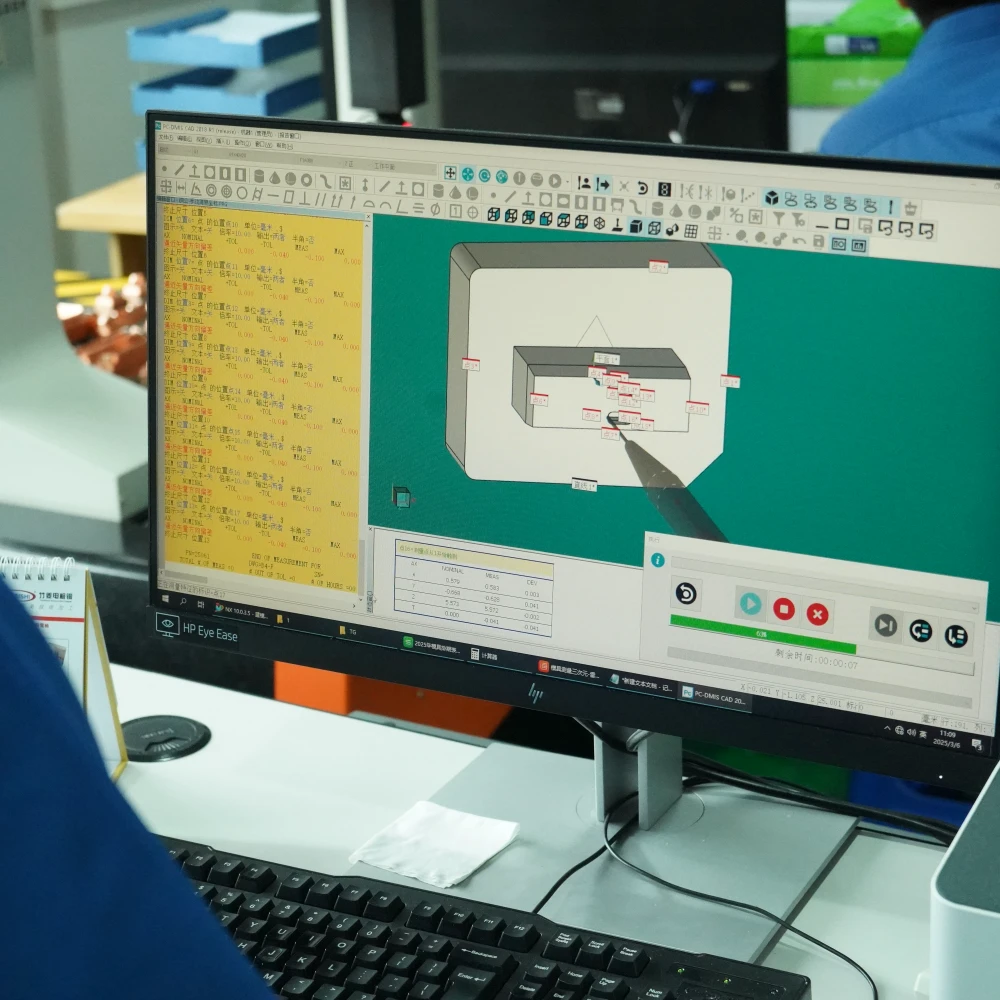
Mistake 2: Compromising on Mold Design Precision
The Issue:
Poorly designed molds lead to inconsistent product quality. A common pitfall is underestimating the impact of mold surface finish (e.g., rough cavities causing visible flow lines) or misaligned parting lines (resulting in flash or burrs).
The Solution:
High-Precision Tooling: Invest in mold design with 5-axis CNC machining (±0.01mm tolerance) to ensure seamless alignment with device features like camera cutouts and buttons.
Surface Finish Standards: Specify mirror polishing (Ra ≤0.025μm) for glossy finishes or textured EDM for grippy surfaces.
Mistake 3: Ignoring Material Compatibility
The Issue:
Choosing materials solely for cost or aesthetics often backfires. For example, generic TPU may yellow under UV exposure, while rigid PC without fiber reinforcement cracks under impact.
The Solution:
Certified Material Selection: Opt for UV-stabilized TPU or glass-fiber-reinforced PC to balance durability and aesthetics.
Compliance Testing: Validate materials against REACH, RoHS, and FDA standards early to avoid last-minute redesigns.
Mistake 4: Underestimating Regulatory Compliance
The Issue:
Non-compliance with regional regulations (e.g., EU RoHS, California Prop 65) can trigger recalls or fines. A frequent oversight is failing to trace material origins or skipping batch testing.
The Solution:
Documentation Systems: Work with manufacturers that provide full material traceability and third-party test reports.
Pre-Production Audits: Conduct compliance checks during pilot runs to catch issues before mass production.
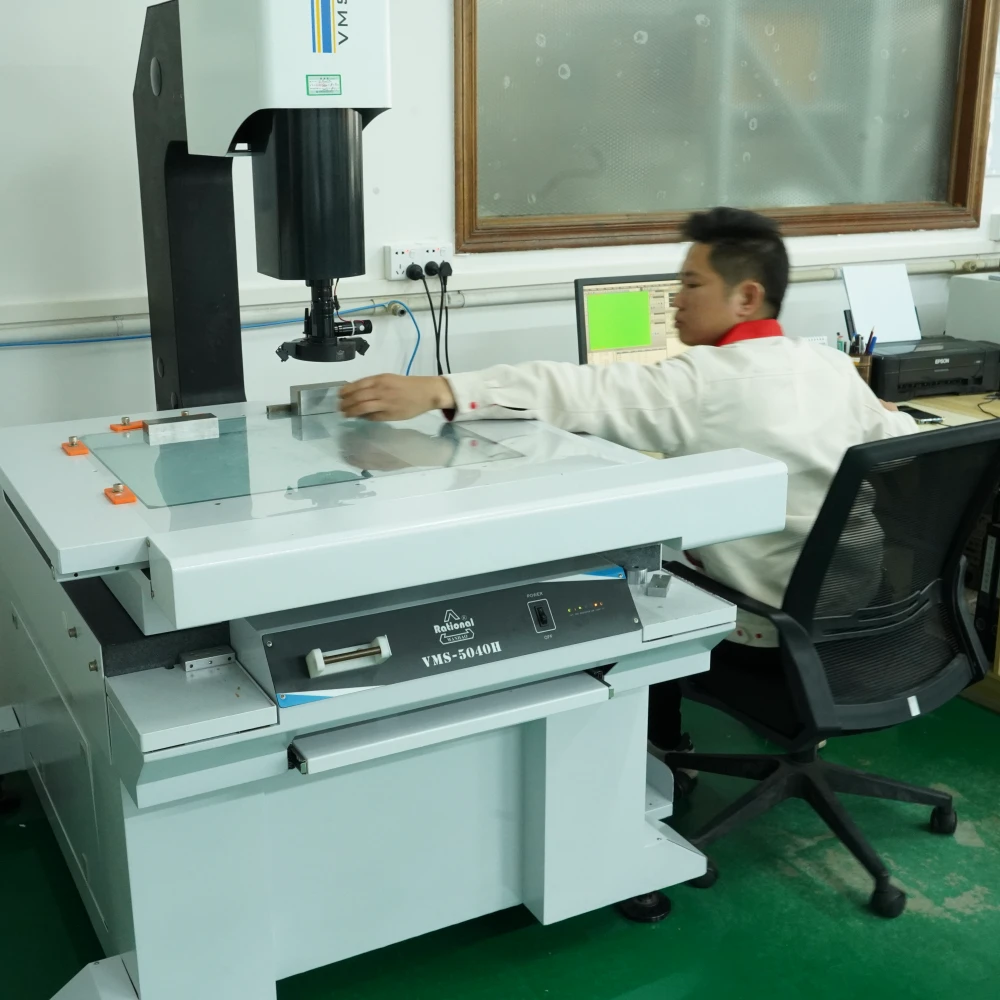
Mistake 5: Skipping Real-World Testing
The Issue:
Relying solely on lab tests (e.g., drop tests under controlled conditions) often misses real-world failure modes, such as long-term wear or exposure to extreme temperatures.
The Solution:
Accelerated Aging Tests: Simulate 12–18 months of use to evaluate color retention and structural integrity.
Field Testing: Distribute beta units to end-users for feedback on grip, button responsiveness, and wireless charging compatibility.
The Path to a Successful Launch
Avoiding these mistakes requires a proactive approach:
Integrate DFM Early: Treat manufacturability as a core design criterion, not an afterthought.
Prioritize Precision: Partner with a phone case manufacturer with proven expertise in mold design and material science.
Validate Relentlessly: Test beyond certifications to ensure real-world performance.
Conclusion
The difference between a successful phone case launch and a costly failure often lies in anticipating manufacturing challenges. By addressing DFM, precision tooling, material selection, compliance, and testing upfront, brands can streamline their journey from prototype to mass production—delivering products that meet both market expectations and quality benchmarks.
Need a Partner to Navigate Your Next Launch?
Consult YG to discuss how to optimize your phone case design for manufacturability and compliance.