As a trusted phone case manufacturer, we combine advanced engineering, stringent quality standards, and flexible customization to create protective and stylish phone cases for global brands. This article unveils the detailed production workflow at our phone case factory, highlighting how we transform raw materials into custom phone cases that meet diverse client demands.
1. Design & Engineering: Where Innovation Meets Functionality
Table of Contents
ToggleAt YG, every custom phone case begins with meticulous design and prototyping.
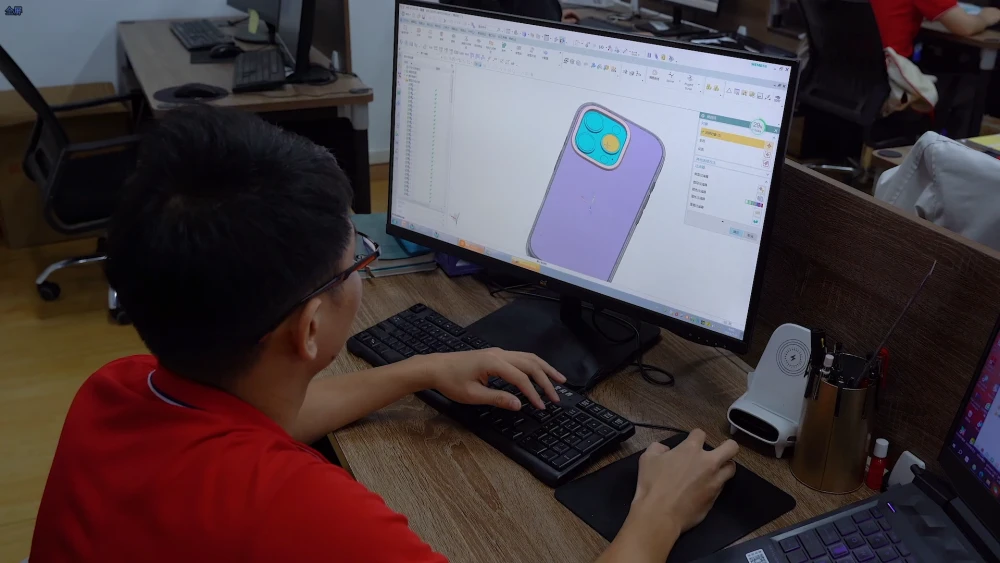
1.1 3D Modeling & Prototyping
Software: Our engineers use SolidWorks and Creo to design cases tailored to specific devices (e.g., iPhone 16.).
Key Features:
Precision Cutouts: 0.3–0.5mm tolerance for ports, buttons, and cameras.
Ergonomic Design: Rounded edges (0.2mm radius) for comfortable grip.
Customization: Add-ons like MagSafe compatibility, card slots, or anti-yellowing coatings.
Rapid Prototyping: SLA 3D printing delivers prototypes within 24 hours for client approval.
Why Choose Us?
As a phone case factory specializing in custom phone cases, we optimize designs for manufacturability, ensuring cost-efficiency without compromising aesthetics.
2. Precision Tooling: The Heart of Manufacturing
High-quality molds are critical for mass-producing consistent phone cases.
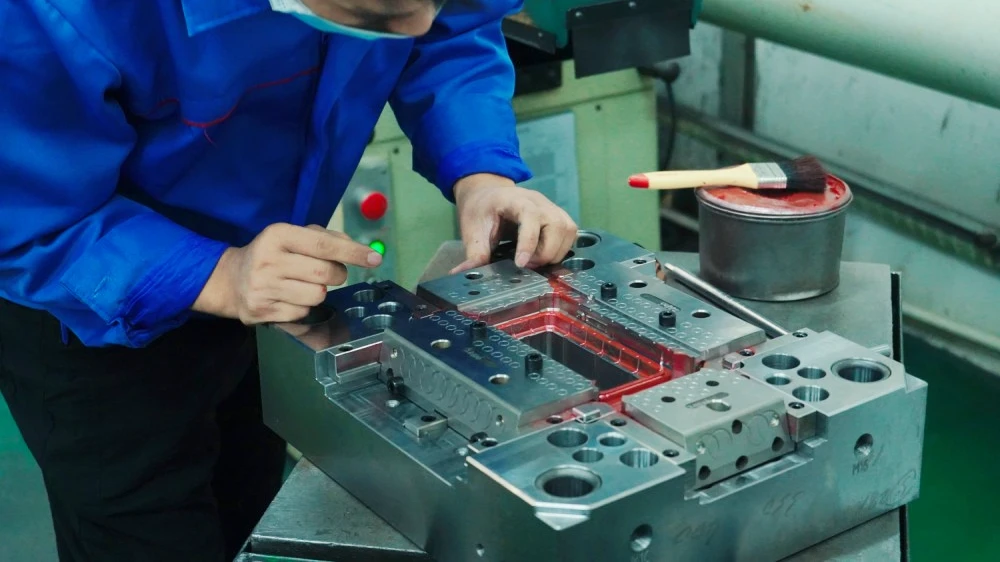
2.1 Mold Manufacturing
Materials:
Plastic Cases: S136 mirror-polished steel (Ra ≤ 0.02μm) for scratch-free surfaces.
Metal Cases: SKD11 hardened steel (HRC 60–62) for CNC machining durability.
Process:
5-axis CNC machining (±0.01mm accuracy) → EDM finishing → Manual polishing.
2.2 Trial Production
Parameter Tuning: Adjust injection pressure (80–120MPa for TPU) and cooling time (12–15s for 1.2mm wall thickness).
Defect Prevention: Solve issues like sink marks (via higher packing pressure) or flash (via mold alignment).
Keyword Integration:
Our phone case factory invests in precision tooling to ensure every custom phone case meets exact specifications.
3. Material Selection: Quality from the Ground Up
We source premium materials to enhance durability and functionality.
3.1 Core Materials
TPU: Bayer Desmopan® 385 (85A hardness, UV-resistant).
Polycarbonate (PC): Sabic Lexan® 943A (92% light transmission).
Aluminum: 6061-T6 alloy (anodized for corrosion resistance).
3.2 Advanced Additives
Anti-Microbial: Agion® silver-ion technology (99.9% bacteria reduction).
Anti-Yellowing: UV stabilizers (e.g., Tinuvin 326) for TPU cases.
For Custom Phone Cases:
Clients can choose specialty materials like biodegradable TPU, Kevlar®, or wood veneers.
4. Production Process: From Raw Material to Finished Product
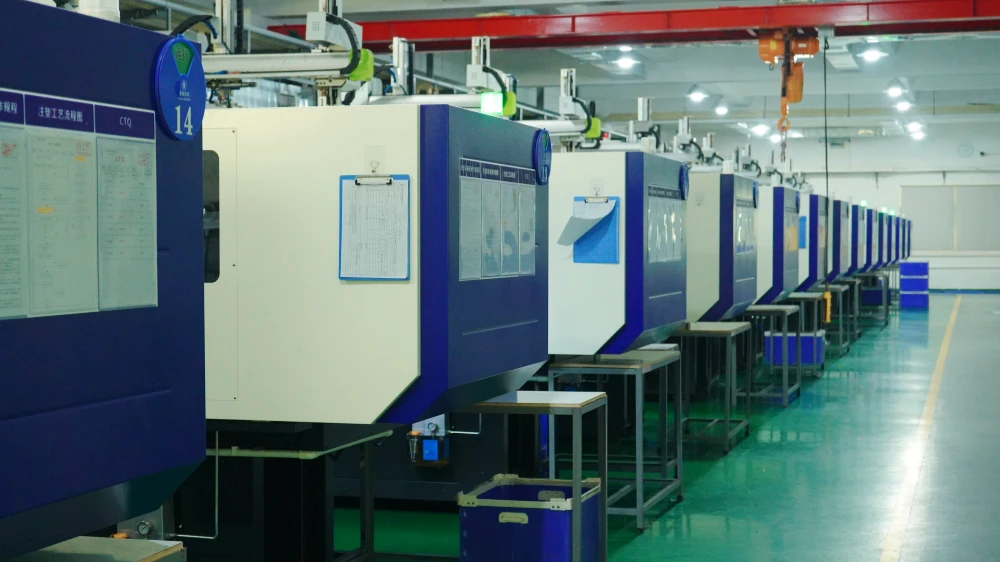
4.1 Plastic Case Manufacturing (Injection Molding)
Step 1: Drying PC/TPU pellets (4 hours at 120°C).
Step 2: Injection molding at 180–220°C (TPU) or 280–320°C (PC).
Step 3: Automated demolding via robotic arms.
4.2 Metal Case Production (CNC Machining)
Step 1: Sheet cutting → 5-axis CNC contouring (±0.02mm accuracy).
Step 2: Deburring via magnetic abrasive finishing (MAF).
Step 3: Anodizing (for colors) or sandblasting (for matte finish).
4.3 Hybrid & Luxury Cases
Carbon Fiber: Compression molding at 150°C/100psi.
Leather Cases: Laser-cut genuine leather bonded to TPU frames.
5. Post-Processing: Perfecting the Details
5.1 Deburring & Surface Finishing
Plastic Cases:
Vibratory tumbling (30–45 mins with ceramic media).
Heat trimming (200°C) for seamless edges.
Metal Cases:
Electrolytic polishing (15A/dm² current density).
5.2 Decoration & Functional Coatings
Printing: IMD/IML for scratch-resistant logos/patterns.
Coatings:
NCVM (non-conductive vacuum metallization) for metallic finishes.
Oleophobic coating (repels fingerprints).
Customization Spotlight:
As a custom phone case manufacturer, we offer laser engraving, UV printing, and embossing for brand-specific designs.
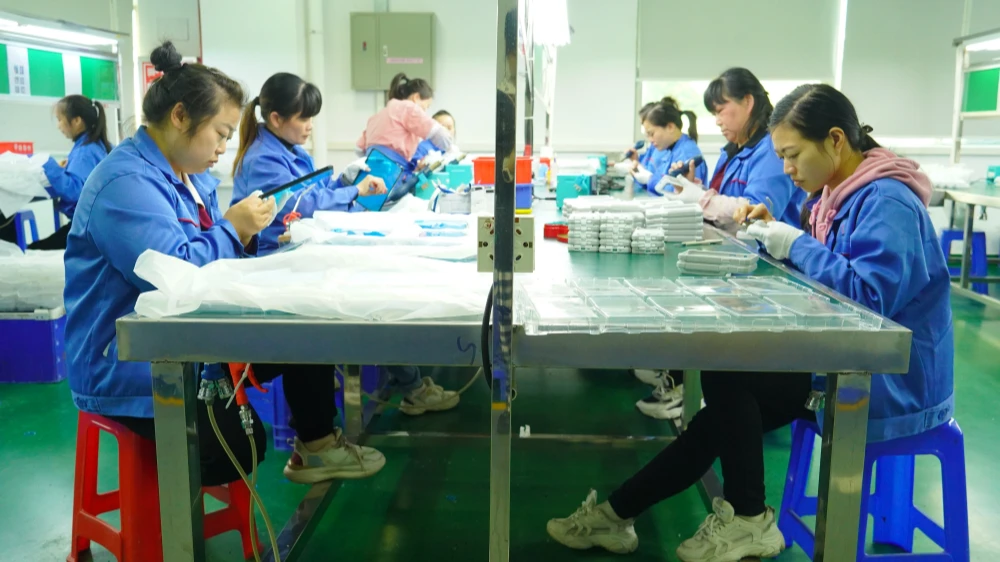
6. Quality Assurance: Excellence in Every Case
6.1 Dimensional Inspection
Tools: CMM (±0.003mm accuracy), digital calipers.
Standards: Button alignment (±0.1mm), thickness uniformity (±0.05mm).
6.2 Functional Testing
Drop Test: 1.2m drops on concrete (MIL-STD-810G compliant).
Wireless Charging: Qi-certified testing (15W compatibility).
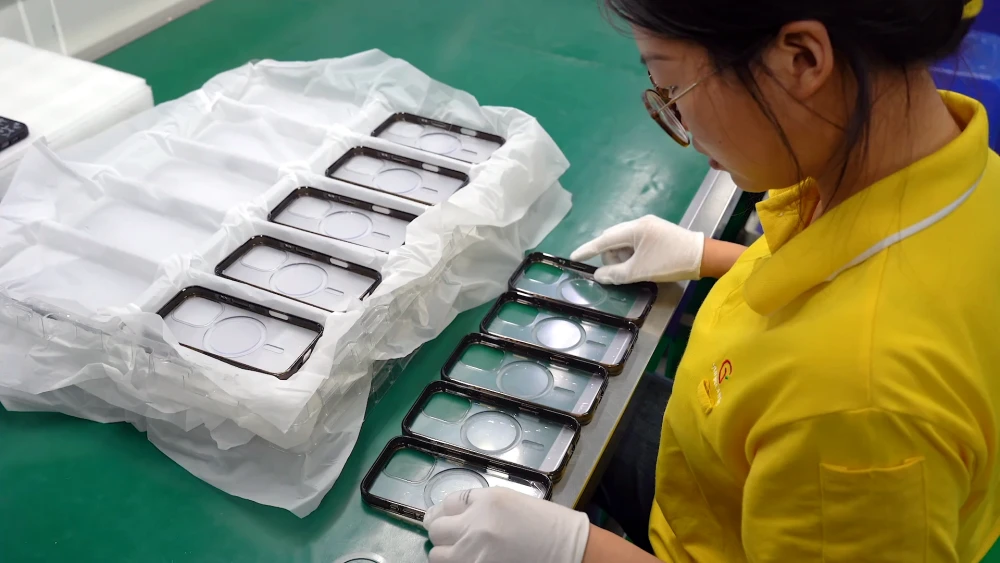
6.3 Aesthetic Checks
Color Consistency: Spectrophotometer (ΔE ≤ 1.5).
Visual Inspection: 100% manual check under D65 lighting.
Keyword Integration:
Our phone case factory’s zero-defect philosophy ensures every custom phone case exceeds industry benchmarks.
7. Sustainable Packaging & Logistics
7.1 Eco-Friendly Packaging
Materials: Recyclable paper boxes, compostable PLA bags.
Labels: QR codes for supply chain transparency.
7.2 Global Shipping
Certifications: RoHS, REACH, CE, FCC.
Efficiency: 15-day lead time for 10,000-unit orders.
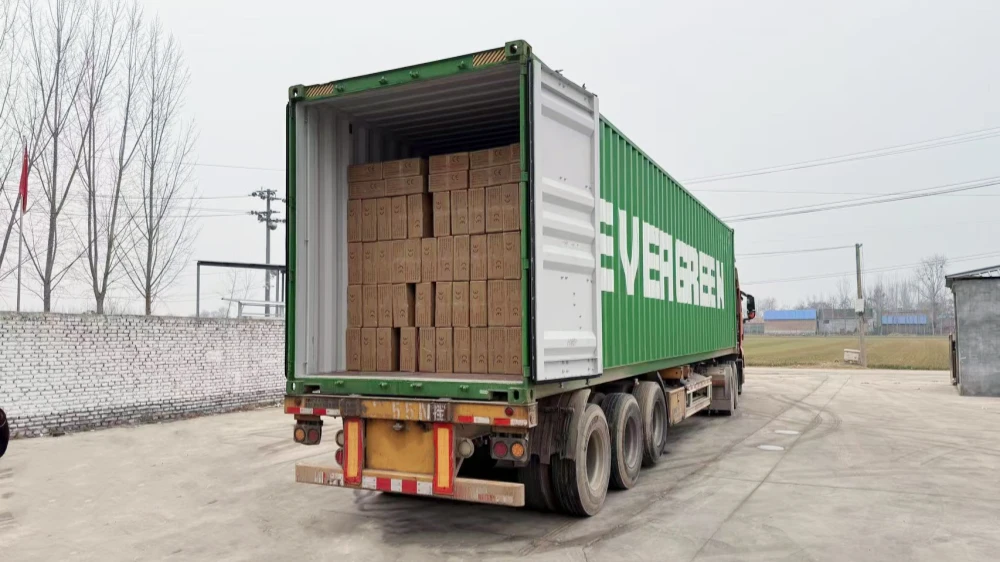
Why Partner with YG?
Expertise: 10+ years as a phone case manufacturer serving Fortune 500 brands.
Technology: Automated production lines (50+ molds/year capacity).
Customization: MOQ 500 units for custom phone cases.
Contact us, your trusted phone case factory, to discuss your custom phone case project today!