The smartphone accessory market will reach $98.3 billion by 2027 (GVR). Yet 73% of procurement managers struggle to find suppliers balancing low MOQ and industrial-scale capacity. At YG, we operate 120 injection molding machines producing 30,000 phone cases daily while maintaining a 500pcs MOQ threshold. This guide reveals how to audit suppliers using 7 operational metrics that truly matter.
Metric 1: MOQ Flexibility vs. Production Scale
Table of Contents
ToggleThe 500pcs Advantage
While most manufacturers enforce 3,000-5,000pcs MOQs, our 500pcs minimum allows:
- Test 5-7 designs simultaneously with ≤$8,500 risk
- 37% faster time-to-market vs industry average
YG’s Capacity:
- Daily output: 30,000 finished cases
- Peak capacity: 850,000 units/month
- Case Study: A U.S. startup ordered 500pcs each of 8 iPhone 16 concept cases, then scaled the top 3 designs to 50,000pcs/month within 6 weeks via our ODM solutions.
Metric 2: Mold Engineering Mastery
150 Molds/Month Precision
With 120 DKK 550-ton injection machines and 31 engineers, we deliver:
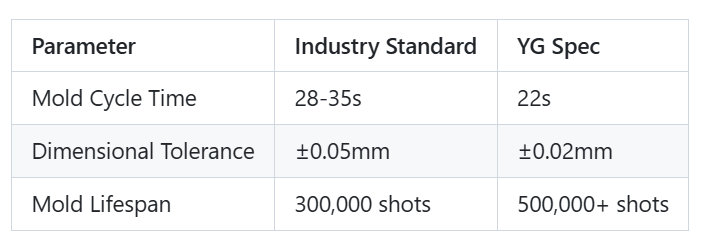
Pro Tip: Ask suppliers for:
- Mold flow analysis reports
- Cooling time optimization data
Metric 3: Certifications Beyond Basics
Compliance as Strategy
We hold 23 certifications including:
- ISO 14001 (Environmental Management)
- ISO 45001 (Occupational Safety)
- Disney FAMA (Licensed Production)
2025-Ready:
- Full documentation for EU’s Digital Product Passport (DPP)
- Conflict Minerals Reporting Template (CMRT) compliance
Metric 4: Customization at Scale
From 500pcs to 500k Units
Our custom phone cases process:
- Design: 24hr 3D rendering (OBJ/STL files)
- Prototyping: 7-day TAT for 500pcs trial orders
- Production:
- 120 machines allocate 15% capacity to small batches
- 48hr material drying → 22s cycle time → 100% AOI inspection
Tech Edge:
- In-mold labeling (IML) for <0.15mm logo precision
- Dual-color molding with 0.08mm interlayer accuracy
Metric 5: Quality Pyramid System
30k/Day Doesn’t Mean Compromise
Our 4-layer QC:
Material
- Shore hardness tests (60D/80A/95A)
- XRF screening for 18 restricted substances
Process
- 120 machines with IoT sensors (±0.5℃ temp control)
- Real-time cavity pressure monitoring
Output
- 100% functional test (buttons/ports alignment)
- AQL 1.0 sampling (Tighter than MIL-STD-105E)
Traceability
- QR code tracking from mold to shipment
Metric 6: Transparent Cost Structure
500pcs Pricing Breakdown
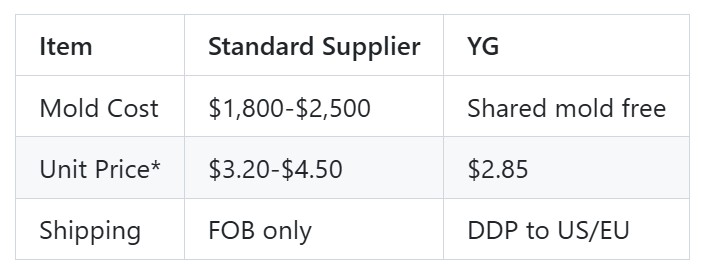
*Based on 500pcs TPU case order
Hidden Cost Savers:
- No charges for ≤3 design revisions
- Free storage for 60 days post-production
Metric 7: Sustainable Scalability
Growth-Ready Partnership
- Phase 1: 500-5,000pcs with 15-day lead time
- Phase 2: 5k-50k/mo with JIT scheduling
- Phase 3: 50k+/mo via dedicated production lines
Client Example:
An Italian brand grew from 500pcs samples to 120,000pcs/month orders with:
- 22% cost reduction through volume incentives
- Dedicated QC team for EU market compliance
Your 2025 Supplier Checklist
- □ MOQ ≤1,000pcs for testing
- □ ≥100 injection machines
- □ Mold lead time <30 days
- □ AQL ≤1.5 certification
- □ Unit cost ≤$3 at 500pcs
Why Global Brands Choose YG
- Speed: 65 molds completed last month
- Precision: 0.02mm tolerance across 120 machines
- Responsiveness: 15min average quote turnaround
Start with 500pcs Risk-Free Samples →
Technical Appendix
Machine Specs:
- Haitian Mars II 550T presses
- 99.2% uptime via predictive maintenance
- Energy consumption: 0.45kW·h/kg (vs. 0.68 industry avg)
Material Options:
- 45+ verified TPU/PC/PMMA formulations
- 18 anti-yellowing grades